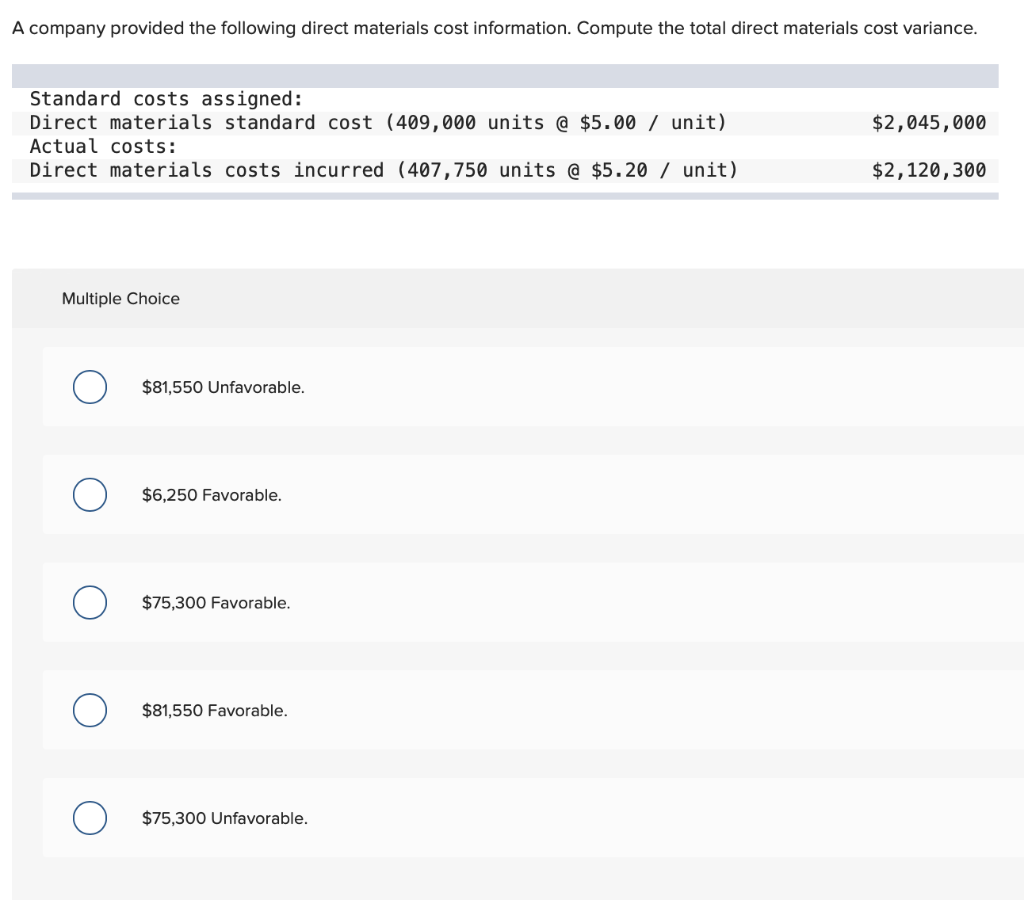
Examples of typical overhead costs are production facility electricity, warehouse rent, and depreciation of equipment. The entities need to properly track their purchase and consumption of direct materials so that they can avoid shortage or unnecessary stock keeping. Shortage of materials may disrupt production as well as cause additional ordering cost to the entity while unnecessary or excessive inventory in stock may lead to materials obsolescence loss. In summary, the purchasing department is often responsible for the price paid for direct materials, as it is directly involved in negotiating and procuring materials and services necessary for the company’s operations. Standard cost is the amount a cost should be under a given set of circumstances.
- Please note that in the employee time tickets that are displayed, each employee worked on more than one job.
- For this reason, labor efficiency variances are generally watched more closely than labor rate variances.
- The final T-account shows the total cost for the raw materials placed into work in process on April 2 (vinyl and ink) and on April 14 (grommets and wood).
Accounting for Manufacturing Overhead
List the expenses necessary to sell pizza and identify them as a fixed cost or variable cost; as a manufacturing cost or sales and administrative costs; and as a direct materials, direct labor, or overhead. For each overhead item, state whether it is an indirect material expense, indirect labor expense, or other. The cost of indirect materials used is added to the entity’s manufacturing overhead cost and, thus, ultimately made part of the total product cost. However, if the amount is significantly minor, the cost of these materials can be directly charged to expense as incurred during a period. The selection from the either approach is largely impacted by the entity’s costing policies.
3: Calculations for Direct Materials and Labor
Cost-based contracts may include a guaranteed maximum, time and materials, or cost reimbursable contract. The training company may charge for the hours worked by instructors in preparation and delivery of the course, plus a fee for the course materials. The unique nature of the products manufactured in a job order costing system makes setting a price even more difficult. For each job, management typically wants to set the price higher than its production cost.
Indirect materials cost
Some items are more difficult to measure per unit, such as adhesives and other materials not directly traceable to the final product. Their costs are assigned to the product as part of manufacturing overhead as indirect materials. Traditional billboards with the design printed on vinyl include direct materials of vinyl and printing ink, plus the framing materials, which consist of wood and grommets.
If we had one favorable and one unfavorable variance, we would subtract the numbers. Do you know of a restaurant that was doing really well until it moved into a larger space? Often this happens because the owners thought their profits could handle the costs of the increased space. Read advice from restaurant owner John Gutekanst about the importance of understanding food costs and his approach to account for these in his pizzeria.
The variance is unfavorable because more materials were used than the standard quantity allowed to complete the job. If the standard quantity allowed had exceeded the quantity actually used, the materials usage variance would have been favorable. Returning to the example of Dinosaur Vinyl’s order for Macs & Cheese’s stadium sign, Figure 4.7 shows the materials requisition form for Job MAC001. This form indicates which department is often responsible for the price paid for direct materials the quantity and specific items to be put into the work in process. It also transfers the cost of those items to the work in process inventory and decreases the raw materials inventory by the same amount. The raw materials inventory department maintains a copy to document the change in inventory levels, and the accounting department maintains a copy to properly assign the costs to the particular job.
The vinyl and ink were used first to print the billboard, and then the billboard went to the finishing department for the grommets and frame, which were moved to work in process after the vinyl and ink. The final T-account shows the total cost for the raw materials placed into work in process on April 2 (vinyl and ink) and on April 14 (grommets and wood). The journal entries to reflect the flow of costs from raw materials to work in process to finished goods are provided in the section describing how to Prepare Journal Entries for a Job Order Cost System. The variance is unfavorable since more hours than the standard number of hours were required to complete the period’s production. These costs are necessary for production but not efficient to assign to individual product production.
The labor efficiency variance occurs when employees use more or less than the standard amount of direct labor-hours to produce a product or complete a process. The three general categories of costs included in manufacturing processes are direct materials, direct labor, and overhead. Note that there are a few exceptions, since some service industries do not have direct material costs, and some automated manufacturing companies do not have direct labor costs. For example, a tax accountant could use a job order costing system during tax season to trace costs.
Materials usage variance Because the standard quantity of materials used in making a product is largely a matter of physical requirements or product specifications, usually the engineering department sets it. But if the quality of materials used varies with price, the accounting and purchasing departments may perform special studies to find the right quality. The amount by which actual cost differs from standard cost is called a variance. When actual costs are less than the standard cost, a cost variance is favorable. When actual costs exceed the standard costs, a cost variance is unfavorable. Do not automatically equate favorable and unfavorable variances with good and bad.